What is a Digital Twin?
Add bookmark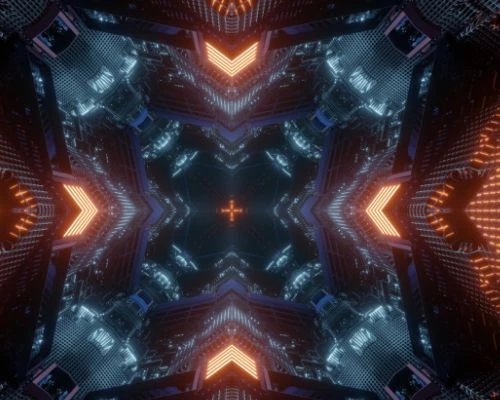
Leading manufacturers have been using digital twins to test product design, identify improvements or risks, and increase productivity. So just what is a digital twin?
A digital twin is simply a virtual representation of a process, machine or other physical object. The digital twin uses data from the real world to represent how the process or object behaves.
This enables a manufacturer to simulate the impact of a potential design or process change before altering the real thing. This is especially important in manufacturing production environments where changes can be costly and can affect production targets.
Ford Motor company, for instance, creates multiple digital twins for each model of car that it produces, according to Palamir. Each twin covers a different aspect of the design, build or operations of each model.
They also use it to model processes in their production facility where the digital twin “accurately detects energy losses and pinpoints areas where energy can be conserved and overall production line performance improved.”
Meanwhile, Chevron is using digital twins for predictive maintenance in its oil fields and refineries and aims to incorporate sensor data from most of its high-value equipment by 2024. The company expects that preventing breakdowns could save millions of dollars each year.
Advances in artificial intelligence and machine learning have made digital twins extremely sophisticated and increase their accuracy. Additionally, the digital twin is an immersive environment and has capabilities that traditional simulation lacks.
As IBM points out, “a simulation typically studies one particular process, a digital twin can itself run any number of useful simulations in order to study multiple processes.”
Digital twins may also be connected to machines in real time via IoT data. This allows for a continuous stream of live production data.
While leading manufacturers may be taking advantage of the capabilities of a digital twin, it has a slightly more “out of this world” origin. Engineers at NASA in the 1960s first came up with the concept to develop a “living model” of the Apollo mission, according to a history on the space agency’s website.
After the 1970 Apollo 13 mission, which saw the spacecraft’s oxygen tank explode (but crew were able to return safely to earth), engineers used a digital twin to evaluate what went wrong.
“The ultimate vision for the digital twin is to create, test and build our equipment in a virtual environment,” says John Vickers, NASA’s leading manufacturing expert and manager of NASA’s National Center for Advanced Manufacturing, quoted in Forbes.
“Only when we get it to where it performs to our requirements do we physically manufacture it. We then want that physical build to tie back to its digital twin through sensors so that the digital twin contains all the information that we could have by inspecting the physical build.”