4 Trends That Will Dominate Manufacturing in 2022
Add bookmark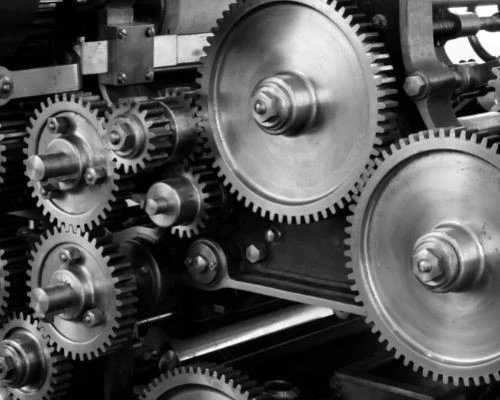
If 2020 was the year of Covid and 2021 was the year of supply chain disruption, what will characterize 2022?
IX Network predicts that sustainability and its alter ego climate change will grab headlines at manufacturers in the year ahead.
Here are the 4 trends you should watch out for as the global economy emerges from the long shadow cast over it by Covid-19 and the world plays ‘whac a mole’ with new variants.
#1: Sustainability Hits the Mainstream
Sustainability has gone beyond compliance and become a board level issue as consumers, governments and investors scrutinize the environmental record of businesses.
According to Gartner, 85% of investors considered ESG factors as part of their investments in 2020.
Many world leaders and governments made dramatic commitments to reduce their country’s carbon emissions at last year’s COP26 summit. Expect a flurry of new legislation, taxes and incentives to come out that will reward those companies that get ahead of the curve and reduce their environmental impact and carbon emission.
International food manufacturer Danone, for instance, is well known for prioritizing sustainability. In February 2020, the company announced a $2.3 billion “climate acceleration plan,” according to McKinsey.
That plan will see widespread changes to the companies operations, energy use, agriculture and packaging to reduce waste and carbon emissions.
“For us, climate is not an externality,” Danone CEO Emmanuel Faber said , quoted by McKinsey. “It’s part of the resilience of our business, so addressing it is not a question of philanthropy—it’s a question of smart business.”
#2: Supply Chain Disruption Made Worse by Climate Change
Supply chain disruption may have initially been triggered by the work from home orders and border closures of the global pandemic, but the extreme weather caused by climate change promises to take disruption to the next level.
One need look no further than the devastation to the road and rail networks that an “atmospheric river” caused in Western Canada a few months ago.
The storm caused widespread damage to critical infrastructure, flooded several regions of the province and cut off normal supply routes.
The city of Vancouver was completely cut off from the rest of Canada. Empty grocery shelves and fuel rationing ensued as damaged supply chains took time to restore.
Meanwhile, more recently, tornadoes that ripped through several US States killed at least 90 people and hit hard in agricultural regions where famers were already struggling to get critical parts and supplies for spring planting.
Extreme events like these have become more likely in recent years. According to the National Oceanic and Atmospheric Administration (NOAA), the total cost of U.S. billion-dollar climate related disasters over the last 5 years (2016-2020) exceeded $600 billion USD.
These major disasters are becoming more frequent. Between 1980-2020, for instance, there was an average of 7 disasters a year with an annual cost of $45 billion per year.
Between 2016-2020 those numbers more than doubled to an average of 16.2 disasters per year causing over $120 billion in inflation adjusted damage annually.
With predictions that extreme weather events will only worsen in the decades ahead manufacturers can expect that supply chain disruption will be a bit like jumping out of the pandemic frying pan and into the climate change fryer.
The new normal is that we’re not getting back to ‘normal.’ Time to draw up your supply chain contingency plans with climate disruption in mind.
#3: Worker Shortage Continues
It’s been dubbed everything from the “Great Resignation” to the “Great Reset” but whatever you want to call it one thing is for certain: there’s too much work and not enough people who want to do it. This cuts across all industries as employees re-evaluate their career and lifestyle changes in the wake of the pandemic.
But, as Stephen Gold, CEO of the Manufacturing Alliance, observed in a recent interview with me, the labor shortage has been hitting manufacturers particularly hard.
“Trying to find employees with the requisite skills to work on shopfloors and to fill R&D departments has become a chronic pain point. The sector has struggled for years to change its image and steer qualified high school and college kids towards their open doors,” he said.
“Manufacturing was already behind the curve when the Great Resignation started, and now it’s got to work doubly hard to start channeling workers to its factories and R&D departments, along with retaining its current talent.”
In the wake of mass layoffs and the perception of manufacturing jobs as dirty and repetitive, it has been hard to attract young people into the industry.
Manufacturers will need to look at improving the sector’s reputation, make life at work stimulating and interesting, and increase wages to attract the next generation of talent.
Additionally, digital tools and automation (see next point) can help to address the immediate shortfalls in labor.
#4: Digital Transformation Revs Into High Gear
As a consequence of the first three trends, we believe that manufacturers will deepen and accelerate their digital transformation plans.
Industry 4.0, which sees a convergence of internet enabled sensors, data analytics, mobile computing platform, robots and process automation, will help manufacturers deal with the challenges of the year ahead.
“In reshaping our world toward a new normal, industry should leverage digital transformation at an accelerated pace. Typically leveraged for productivity, digital transformation is equally effective in achieving economic and environmental resilience,” write authors from Rockwell Automation in an article published on the World Economic Forum.
“To capitalize on the convergence of Industry 4.0 and ESG goals, industry leaders must enable operational efficiency, leverage renewable energy, practice life cycle thinking, and promote supply chain data transparency.”
Robots and process automation, for instance, can help manufacturers respond to the shortage of staff by enabling them to free up precious labour for the tasks that can’t be automated.
Meanwhile, as we write in The Disappearing Manufacturing Worker, Connected Worker Technology can improve employee morale and training, which helps with onboarding, productivity and retention.