Towards a Digital Future at RS Group
Add bookmark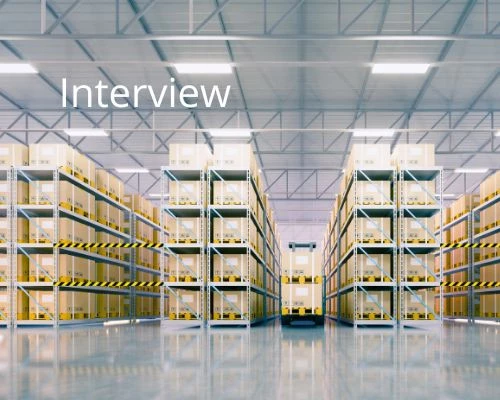
RS Group is a global omni-channel provider of product and service solutions for designers, builders and maintainers of industrial equipment and operations. With over 1.2 million customers and operations in 32 countries, it supplies the critical components needed to keep the wheels of the global economy moving.
The company has more than 700,000 stocked and three million unstocked high-quality industrial and electronic products from over 2,500 suppliers, and is now expanding its range of safety solutions following the acquisition of Needlers and Liscombe, suppliers of industrial safety and personal protective equipment (PPE).
The products may be industrial, but the company’s offerings are taking a decidedly digital turn.
In this interview, John Barnacle-Bowd, Vice President Global Environment, Health & Safety at RS Group discusses the impact of digital transformation on his company, observations from two decades working in heath and safety, and what’s on his agenda in the year ahead.
Diana Davis, IX Network: We are seeing so much digital change now. How has digital transformation been affecting you at RS Group?
John Barnacle-Bowd, RS Group: Our customers are becoming more demanding, wanting ease of use, hyper-personalisation and a ‘faster than real-time’ experience.
Our omni-channel offer ensures we serve our customers through the most appropriate channel to give them a personal, efficient and differentiated experience.
We deliver a technology-enabled offer with a human touch and 62% of our revenue comes through digital channels.
Today, our customers know that they can trust RS to provide them with the tools and equipment they need and when they need it. By offering innovative solutions for their procurement, maintenance, and inventory needs, we can also help add value and cost-savings.
Diana Davis, IX Network: How does that help reduce costs?
John Barnacle-Bowd, RS Group: We have a broad range of supplier brands, giving our customers the very best choice when it comes to the products they need, however, true cost-saving starts with our service solutions.
Our aim is to help our customers manage their indirect spend more effectively and make their lives easier with our product knowledge and technical expertise, using data and digital excellence.
Regarding procurement, we offer solutions for customers to consolidate their spend and reduce procure-to-pay costs, providing continued cost efficiencies across eProcurement solutions, RS ConnectPoint™ and systems such as IESA’s marketplace platform, MyMRO.
Our range of solutions, such as RS VendStock™ and RS ScanStock™, as well as IESA’s and Synovos' fully outsourced inventory management, enables customers to manage their inventory more effectively, reducing working capital and improving productivity.
We provide maintenance solutions to help customers manage their assets and improve productivity and sustainability. We also offer product-specific knowledge and services such as calibration, energy monitoring and condition monitoring.
Diana Davis, IX Network: Speaking about your role specifically. You're in HSE (Health, Safety and Environment). How does digital impact your role?
John Barnacle-Bowd, RS Group: We’ve tried to digitize some of the ways in which we assess the ergonomic risk that our warehouse employees face. For instance, we started using a system called DorsaVi about five years ago. The system tries to digitize and quantify the ergonomic risk that workers face. But unfortunately, we had to stop using that system during Covid.
We’ve also started using QR codes to report near misses. However, we have certain restrictions on how employees can use mobile phones when they're in the warehouse, and that makes it harder to digitize. So, most of our accident reporting itself is still very much based on phone calls and Excel spreadsheets.
READ: Safety Management Systems: Building a Foundation on Data
Diana Davis, IX Network: How does the QR code work for reporting near misses?
John Barnacle-Bowd, RS Group: Basically, the worker scans the code, and it brings up a form on their phone and they fill in a few basic fields with the relevant information.
I’m all about making stuff easy because if it’s easy, people will do it. If it’s not, they won’t.
Once they fill in the form, they press enter and it automatically goes to a central location where it is collated, and imported once a month to the group. It’s very simple but we’re looking at how we can use more of these simple and relevant digital tools.
Diana Davis, IX Network: I've often heard that when you're tackling digital, you need to take small achievable steps in the right direction rather than go for the big bang. It sounds like your QR code is like that?
John Barnacle-Bowd, RS Group: That’s right. One of the first places we rolled out the QR code was in APAC because historically near miss and accident reporting is low in that region. I don’t want accidents, but I do want people to be honest and report them.
We started with the near miss reporting. This includes unsafe conditions, unsafe acts, and actual near misses. These are all opportunities for improvement.
I wanted to start seeing those from APAC as we’ve got a great reporting culture in other markets, but it was weaker in APAC.
The culture in APAC isn't really geared towards reporting safety incidents because there is fear that perhaps it was the individual’s fault, or that it may reflect badly on their supervisor. Employees in APAC don’t want to make their supervisors look bad, so there is a cultural piece that can be difficult to get across.
We're trying to bridge that gap and it seems to be working now. It helps that the team member who came up with the QR code idea happened to be based in Hong Kong.
READ: 6 Technologies that are Redefining How Companies Manage Worker Safety
Diana Davis, IX Network: Are there certain technologies that you're looking at you think will apply in the HSE environment?
John Barnacle-Bowd, RS Group: I would love to use AR as part of our induction or training, but we’d need to look at this in more detail and what we’d use it for.
Diana Davis, IX Network: What advice would you give to someone starting out in the HSE field?
John Barnacle-Bowd, RS Group: I’d say to ‘give it a go.’ It may not seem like the most exciting career choice, but it holds opportunities if you want to make a difference and keep people safe.
Don’t go for the easy option. It’s most interesting to work in industries where you can make the biggest difference. If you go to an industry that’s safe and boring, you’ll likely get bored.
How do you stop accidents happening again? What do you learn from them? And then how do you take that learning forward to share that with others?
Thankfully, we tend not to see too many nasty accidents anymore, but each company and industry has its own challenges. My current industry is safer because we’re in a controlled environment in the warehouse with constant supervision.
It can be more challenging to enforce safety standards if you have an independent operator that goes to a customer site to do work, for instance. You need to rely upon them to keep themselves safe and judge situations.
The other thing I’d add is that with the increasing focus on sustainability, there’s a whole different set of skills that I think we need.
Although I’ve done environmental management systems in the business for the last 10-15 years, sustainability is all very new to me. We’re looking at all sorts of things such as what is the best vehicle technology for our company cars? Should we go hybrid? Should we go all electric? When will we do this by?
We now have a goal to be net zero by 2030 in our scope one and two emissions. The big question is how are we going to get there?
Luckily our Board is engaged and our CFO is very keen on it. We have a new VP of social responsibility and sustainability who joined us from Centrica and has lots of great ideas. We have the leadership we need in place to achieve it, which is important.
Diana Davis, IX Network: Final question, what's your focus in the year ahead?
John Barnacle-Bowd, RS Group: Improving our safety. During Covid our accident rate increased slightly after falling for several years. I don’t think it was a direct result of Covid because, ironically, during the pandemic we have had an increased awareness of health and safety.
It’s hard to pin it why the accidents increased on any single factor, but I think fundamentally it comes down to change. Whenever change happens, accidents typically go up.
For instance, at one of our largest distribution centers, we doubled its size, added a brand-new management team and about 150 new employees. Accidents did increase at the facility in the first year.
It’s something we are really watching as we acquire new companies to ensure that our safety programs mitigate those risks.
Interested in learning more about this topic?
Join over 200 industry leaders on November 15-17, 2022 at our Connected Worker conference in Chicago and learn how to build a connected workforce to improve resilience, agility and growth in a recovering economy. Download the agenda here.