ASME Report: Industry 4.0 Requires Engineering Skills Rethink
Add bookmark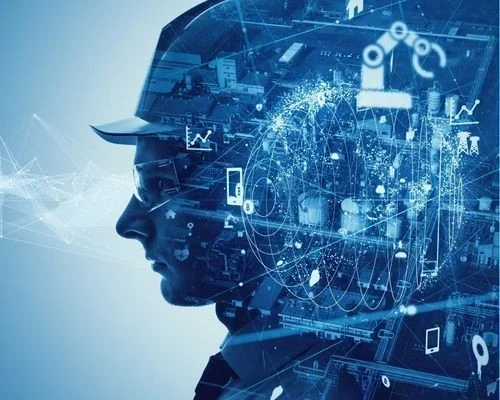
There are more manufacturing jobs out there than there are skilled people to fill them, according to Ashley Huderson, Director of Education and Outreach at the American Society of Mechanical Engineers (ASME). The problem is only set to worsen if nothing is done to address a growing disconnect between workers and the skills that industry requires.
“We are facing an under-skilled workforce that may not be able to execute the work needed and, therefore, they cannot produce the business results you need,” says Huderson.
“Ultimately, to obtain higher productivity, profitability and time-to-market, you’ll need a skilled workforce that can apply the latest technologies to improve how you run your business and help you build your unique competitive advantage,” she says.
How can manufacturers and academia address that disconnect to build the workforce of the future?
That was one of the questions that Huderson and her collaborators sought to answer in a new report on the “Future of Manufacturing.”
The report, a collaboration between ASME and Autodesk, Inc. identified key technical skills that the mechanical and manufacturing engineers and machinists of the future will be expected to know. These include skills in emerging technologies such as artificial intelligence and machine learning, design for manufacturing (DfM), data analytics and management, operations technology infrastructure, and integrated software platforms.
The report also highlights the continued importance of soft skills such as communication, problem solving, and interdisciplinary understanding. Indeed, according to Huderson, cross disciplinary understanding will be one of the most important skills of the future.
In this interview, Huderson and Simon Leigh, Senior Manager Global Education Strategy at Autodesk, discuss the research findings and what they think are its most important take aways.
Diana Davis, IX Network: Why did you think this research was particularly important to do now?
Ashley Huderson, ASME: This research is important because there are more jobs than manufacturing professionals, so job seekers are getting jobs without, necessarily, all the skills training needed.
It was critical that we not only examine the skills needed for these jobs now, but also what is coming down the pipeline in terms of skills and workflows needed for future jobs.
Currently, we are facing an under-skilled workforce that may not be able to execute the work needed and, therefore, they cannot produce the business results you need. Ultimately, to obtain higher productivity, profitability, and time-to-market, you’ll need a skilled workforce that can apply the latest technologies to improve how you run your business and help you build your unique competitive advantage.
That skilled workforce will need educational institutions to start them off with the right skills as well as reskill and keep them trained to advance in their careers. If we don’t align education with changes in technology and industry, skills gaps are just going to widen.
Diana Davis, IX Network: Could you take us through what you think are the most important findings?
Ashley Huderson, ASME: We examined and identified the future workflows and skills needed for mechanical engineering, manufacturing engineering, and CNC machinist roles over the next decade. Each role will evolve in its own way, but the study shows that the necessary new skills will consist of a purposeful combination of common skills (both hard and soft skills) that apply to all three positions, and interdisciplinary skills.
Our key finds included:
- Shifts in job functions and skills, surrounding in all three areas around converged cloud and data platforms (e.g., integrated CAD/CAM), AI/ML applications, generative design, data analytics, AM, and co-botics.
- The impact of soft skills on all three focus areas. Things such as enhanced communication skills and cross discipline understanding were prominent in our results.
- Industry can contribute to growing the skills of the manufacturing workforce of the future through internships and co-op programs, robust internal training, and development, embracing and reinforcing the need for manufacturing workers to engage in continual education, and partnering with and supporting education institutions (particularly community colleges) by serving on advisory boards and as faculty members.
- Engineering academics can start to rethink engineering education from the ground up. They know they must incorporate more practical, “hands on” learning opportunities for their students to fully grasp design-for-manufacturing knowledge and skills.
Diana Davis, IX Network: Was there anything that surprised you?
Ashley Huderson, ASME: Nothing surprised me, but it was comforting to see that both industry and academia understand the need for this work as well as the need for changes. We often see a disconnect between industry and academia, especially when it comes to emerging technologies and how to train students to engage with those technologies.
This work showed that both stakeholders understand that we need pivots in curriculum as well as job training to prepare for the future.
Diana Davis, IX Network: There’s a great phrase you use in the report: reducing “time to talent.” It seems particularly relevant now in the era of labor shortages and the great resignation. What are the most important skills that you think manufacturers should be looking to embed within their engineering teams to position themselves for the future?
Simon Leigh, Autodesk: What we found was that as the rate of technology change increases in the era of Industry 4.0, companies are sometimes overlooking the role of new workflows. Technology is what grabs the headlines.
But it’s really important not to forget that workflows need to evolve. Roles that were traditionally very distinct, like designer, manufacturer, and CNC programmer, need to converge. Manufacturing engineers, for instance, need to get more involved in the mechanical engineering process or design process up front to bring their skills and their knowledge to that process.
Soft skills such as communication and leadership are going to be hugely important in this process. So, while technical skills will certainly be important as Industry 4.0 progresses, our research found that there is still a big place for those soft skills in the workplace.
Diana Davis, IX Network: Ashley, is there anything you’d like to add to what Simon has said?
Ashley Huderson, ASME: I think cross-pollination, exposure to, and interaction with, different disciplines and teams are among the most important skills. These can be achieved via frequent job and project rotation and as well as indigenous training solutions.
Gone are the days of silos. Academia as well as industry needs to train and implement, through practice, this concept of cross-pollination/interdisciplinary engineering work.
Diana Davis, IX Network: The recognition that we need to break down silos has been around for decades but achieving it is difficult. Are there any companies that you encountered that were having success with more of an interdisciplinary approach?
Ashley Huderson, ASME: I won’t call out specific companies (for fear of missing some), but I will say that companies are seeing the benefits of having engineers who have a working understanding of the entire ecosystem from a 3000 ft view rather than the engineer who only knows their work. Being able to understand how your work fits into the entire equation helps with troubleshooting, problem solving, and strategizing.
Diana Davis, IX Network: What do you hope manufacturers and engineers take away from the report?
Ashley Huderson, ASME: I hope the urgency for change and the need for collaboration is a major take away.
When we look at training the workforce for Industry 4.0, there are several key contributors. These include education institutions, industry, and technology companies.
These three contributors must work together to ensure students have the correct skillset to be successful in Industry 4.0. They form an “education ecosystem” that has continuous and open lines of communication.
As we move further into Industry 4.0, it will be critical for all three parties to be involved in the workforce development process. Industry can share best practices and key insights to help with curriculum and technology development. Technology partners can provide not only the tools needed, but also the learning resources, certifications, and workshops to prepare students, faculty, and commercial customers for the ever-evolving workforce requirements of Industry 4.0.
Finally, education institutions can combine resources and insights from technology and industry partners to refresh and create curriculum to match the new requirements of Industry 4.0. It will certainly be a team effort that requires collaboration between these stakeholder groups through the entire process.
Simon Leigh, Autodesk: I’d add that we saw a shared interest in moving forward from both manufacturing engineers and educators.
We often hear that educators don’t speak to industry enough. But we saw both parties seek to understand these future skills, future workflows, and future technologies so that we can better prepare and equip students and others, to become the workforce of the future.
The real take away for me is that there is alignment. However, there is still some work to do to ensure that curriculums are aligned with the skills that we will need in the future.