Ford's Industry 4.0 Specialist on Successful Strategies for Digital Transformation
Add bookmark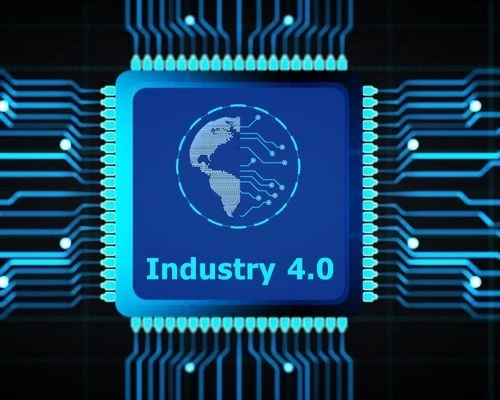
Manufacturing companies have sought for years to harness the productivity and quality gains that can come from the implementation of an Industry 4.0 strategies. Smart new digital technologies such as artificial intelligence, wearables, IIOT, and others, have offered manufacturers unprecedented insight into their operations.
But whether you’re just embarking on a new Industry 4.0 journey or have been reaping the benefits of technology for years, there’s always more to do, says Seonhi Ro, Industry 4.0 specialist at Ford Motor Company.
“I don’t think you can ever finish your work with Industry 4.0,” she observes. “You can always push one step further in what you are doing.”
In this interview Ro shares her insight on what it takes to successfully implement Industry 4.0 strategies, elements you need to consider and her top advice to companies just getting started on their journey.
Diana Davis, IX Network: You’re an Industry 4.0 specialist at Ford. What does that mean? What does that look like at Ford?
Seonhi Ro, Ford Motor Company: To give it a general definition, Industry 4.0 is the cyber-physical system where we connect people and things with information.
In the automotive industry, we’ve been very well connected for a long time. Our operating systems - with most of our productivity data - was connected as well as our quality and maintenance systems.
At the high level most of our systems were connected.
But if you go down to the level of the machines, you find that the machines have a lot of data that was not connected to the central network. The machine has information about downtime, productivity, temperature, etc.
There was a separate control system for these machines but it was not connected to the central networks.
We are now connecting these machines to the network. But there are trade-offs. You cannot do everything at once if you’re retrofitting existing sites.
If you’re building from scratch, it’s easier to get everything connected. However, we have a lot of brownfield sites where we need to connect legacy machines.
Diana Davis, IX Network: How are you going about that process? How are you prioritizing what to do first?
Seonhi Ro, Ford Motor Company: We are prioritizing the areas where we expect to see the greatest benefits. We’re looking at cost to value and prioritizing those sites that have the strongest business case.
Our plants are going and connecting to a global data base together. That allows them to benchmark. But it was important to establish that we weren’t just doing it so that management could determine the best plant.
Every plant is different. It’s important to have the bigger context when you’re evaluating performance across plants.
Where benchmarking helps is when you have the same equipment in different plants. Then you can do some comparison and get the plants to start talking to each other to share ideas.
Diana Davis, IX Network: It sounds like Ford already had a very strong culture in place to enable Industry 4.0. What would you say are the elements you need to have in place culturally before you can enable that digital transformation?
Seonhi Ro, Ford Motor Company: The mindset of the people takes most of the time and is the most important.
Many workers have a fear of automation. They see machines coming in and are worried that they will lose their job. You need to explain that this is not the case and that they need to work together with the system and analytics people.
The other thing is that while it is important for management to see the data, you have to remember that what management needs is very different to what the operator needs. You have the same data but you need well designed interfaces where each user can see only their data.
You really need to think through that.
It’s easy to sink a lot of money in projects like these and not get the results you are expecting if you don’t have that mindset or right approach.
A common problem is that you bring a lot of different people together and run these Industry 4.0 projects. But the first time all the different groups come together, they don’t really understand each other. They didn’t speak the same “language.”
My first role was to translate so that everyone understood what we were talking about: “what you are saying is this…”, “what you’re talking about means that…”.
It’s also crucial to get the operator involved. You get better results because they’ve worked through the details with you and don’t need training on the applications.
But in terms of the mindset, if you get people involved and they see the success, they get motivated and contribute more ideas from different places. That’s what really gives momentum for the whole organization.
Diana Davis, IX Network: What advice would you offer to companies that are just getting started with their Industry 4.0 strategy?
Seonhi Ro, Ford Motor Company: The important thing is to have the big picture on where you’re going. It’s just like when you set out on a car journey. You need to have the destination in mind and then travel kilometre by kilometre to get there.
What I see if that a lot of companies try to start and think the next day they’ll have mastered it. But it doesn’t work like that. People need to come together; the operators need to have control.
At each step, a lot of people ask whether we’ve finished the installation. I don’t think you can ever finish your work with Industry 4.0. Each step has different levels.
Once you’ve started collecting data, for instance, you need to start using it. You can analyze it, perform root cause analysis and then take action on the data. You can have predictions to avoid failures. You can always push one step further in what you are doing.