Balancing Global Standards with Local Innovation
Add bookmark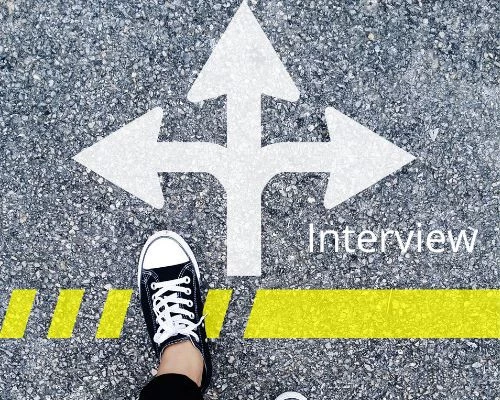
It's a challenge that all multi-site manufacturers face. On the one hand, you want to ensure that all your plants adopt best practices. On the other hand, your customers want a consistent product or service no matter where produced.
However, too strict a focus on standardization can reduce the chance of a local operator finding a breakthrough improvement that takes performance to the next level.
How do you implement consistent, standard management practices without stifling autonomy and innovation?
Morgan Advanced Materials, an industrial component manufacturer, operates plants worldwide.
Suranjan Ghosh is Global Operations Director, Thermal Products Division at Morgan Advanced Materials, overseeing manufacturing on 5 continents. He knows first-hand the challenges of striking a balance between establishing international standards while still giving local operators the space to innovate.
"It can be a challenge to get people to move consistently forward in the same direction at the same time while allowing your people the autonomy to adapt the standards to fit their needs better," he explains.
Ghosh discusses balancing consistency with local innovation across their global manufacturing footprint in this interview. Additionally, the two questions he asks to encourage knowledge sharing of best practices and explain why he believes connected worker technology means using data to drive the right behaviours.
Diana Davis, IX Network: We've seen digital technology transform many manufacturing companies, particularly in the last couple of years. In what ways has digital affected your operations at Morgan Advanced Materials?
Suranjan Ghosh, Morgan Advanced Materials: As with many companies, we are also looking at how best to employ technologies, especially digital, to help us get better at serving our customers. I have to add that keeping our customers in the centre of what we do is something Morgan has been doing for over 165 years.
These technologies can have a different impact – simple examples could include more online collaboration across regions and functions, sensors to give more real-time data, and better systems and processes to gain actionable insights and deliver change.
All of these are aligned with our purpose of helping our customers use our advanced materials to make the world more sustainable and improve the quality of life.
WATCH: The Importance of the Connected Worker in Ensuring Resilience in a Post-Covid World
Diana Davis, IX Network: You oversee 22 sites for the Thermal Ceramics division operating globally in your role. What are the biggest challenges of managing such a diverse operation?
Suranjan Ghosh, Morgan Advanced Materials: I would say it is a privilege to manage such geographically diverse operations. Not many jobs offer this range of diversity, and I am grateful for it.
If I have to look at it as a challenge, then perhaps I would say, it is about how we keep everyone connected and moving forward as a team. It's about how we can provide more localized service yet maintain global standards.
On a lighter note, I would add that a challenge is having the middle of the day jam-packed in my diary, as that's the best time to get some of our global colleagues for calls. I am grateful that I am located in the UK (or Europe), which is excellent from a time zone viewpoint.
Diana Davis, IX Network: How do you balance standardization with the ability to innovate in the sites?
Suranjan Ghosh, Morgan Advanced Materials: There is no magic solution – it’s about team engagement and communication.
We are using technology to share, from video calls to videos, from sharing information to having processes. We do have to benchmark and best practice sharing calls. However, I would say it’s more cultural – constantly creating a culture where we can collaborate, share, and improve on others’ ideas.
Diana Davis, IX Network: We are hearing much more about connected worker technology to address labour shortages. Connecting workers to information and resources in the workflow can quickly get recruits up to speed and improve productivity among existing staff. Is connected worker technology something you have implemented or are looking at in Morgan Materials?
Suranjan Ghosh, Morgan Advanced Materials: Rise of the connected worker is a great title for a blockbuster movie.
Ok, jokes aside, I’d like to fall back to basics – you and I have had digital technologies change our lives. In the last decade, we have used digital tools more. Be it banking, shopping or watching movies. As a result, we have had to learn new working methods and change ourselves.
Connected worker technology, at its core, is about helping everyone within the value chain to have more technology at their disposal to make things easier. So operators who had to fill data into paper forms could use the capability in their phones, rather than record information, they can share insights globally faster.
Yes, this is something that we are working on, but it is about approaching what we want to change, how we want to change it and at what rate we want to change it to serve our customers best but also enable our people to make the change.
WATCH: Creating and Sustaining a High Reliability Culture embedded in Lean Principles
Diana Davis, IX Network: Have you learned any lessons so far?
Suranjan Ghosh, Morgan Advanced Materials: We are working on several different things. Some of these can be scaled up and implemented across the different operations.
Key learning – focus on value. Note that value does not always mean money that brings the most significant advantage to our operations. It could be automation that improves ergonomic issues. And focus on how we can help people through the change process. So value and helping people through the change are the two essential things.
Diana Davis, IX Network: What is your focus in the year ahead?
Suranjan Ghosh, Morgan Advanced Materials: If there is one thing that we should have learned from the last few years is that change (pandemic, supply chain issues, the desire to reach net zero, the conflict in Ukraine), a lot of which is unpredictable, is going to happen.
So the focus for me, at least, is our people. How do we work with our employees to make us resilient and adopt change? I suppose it is kind of Darwinian to say its ability to cope with change will help us evolve. So technology is an enabler, but I would be focusing on our people and how we are best positioned to adopt and adapt to the technology.
Interested in learning more about this topic?
Build a data-driven, connected workforce that will drive continuous improvement across your enterprise. Join over 200 industry leaders on November 15-17, 2022 at our Connected Worker conference in Chicago and learn how to build a connected workforce to improve resilience, agility and growth in a recovering economy. Download the agenda here.