Developing the Skills and Culture Needed for Industry 5.0
Add bookmark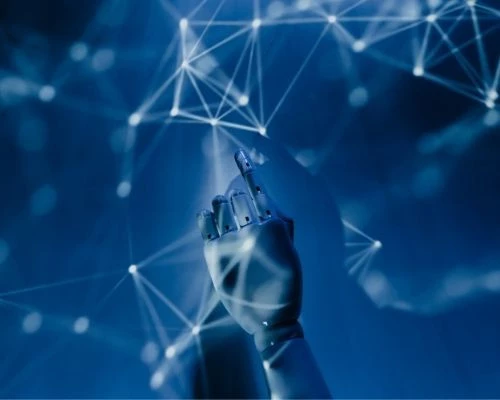
The next generation of workers need skills that focus on learning, innovation, and thinking, says David Crawley, Professor of Practice in Technology Leadership & Innovation Management at the University of Houston College of Technology.
But, he adds, most organizations fall woefully short on establishing these competencies.
“We’ve tended to build a workforce based on the skills of doing a particular job, which insulates talent into hardened silos of tasks,” he says.
That needs to change as manufacturers deal with the increasing complexity and technological disruption of Industry 5.0. Robots, artificial intelligence, sensors, and automation are among the many factors rapidly changing the nature of work at modern manufacturers.
In this interview, Crawley discusses the challenges of Industry 5.0, how companies need to respond to changing technological development and population demographics, and offers his advice on what it will take to develop the right set of skills and culture for the future.
Diana Davis, IX Network: I have just started to get my head around Industry 4.0 and now many experts say we are heading to Industry 5.0. What is Industry 5.0?
David Crawley: Industry 4.0 is all about efficiency for doing things faster and better. The dynamic is to compress time and deliver more information so workers can make better decisions.
Industry 5.0 is an evolution of that. It is inundated with artificial intelligence, robots, and automation. This increases the speed at which people are getting information.
Now there is so much information that is coming through. Information flows through to everybody from the worker on the shop floor up to the Chief Executive Officer. The workforce is saturated with data, and workers are challenged to know what questions to ask.
The challenge for companies, is that we don't have a workforce that is prepared to accommodate and scale the digital solutions that guide decisions that are coming down the pipeline.
As an example, we are doing work with oil companies where they are deploying AI at the wellhead for preventive maintenance in compressors and other equipment. But they tell us that they are getting so much information that they don’t know what to focus on first. They do not know what to do with most of the information they get.
Diana Davis, IX Network: So, is it just a matter of learning to break down data into questions?
David Crawley: That is certainly one methodology that needs to be deployed. But it’s bigger than that. The World Economic Forum has produced a list of critical skills that organizations will need in the years ahead. Innovation is number one on the list, followed by active learning, complex problem solving, critical thinking, lateral thinking, logic modeling, systems thinking, communications, and leadership. Unfortunately, there has been insufficient time spent building a workforce with these skills. We have tended to build a workforce based on the skills of doing a particular job, which insulates talent into hardened silos of tasks.
And it shows. Nearly three quarters of global executives in the GE Global Innovation Barometer indicated that their biggest concern is that they feel that the lack of innovation skills is impeding their company’s ability to be competitive.
It is widely known that workforce skills degrade by half every six years if they’re not constantly training and upskilling them. This is especially important with Industry 5.0 beating on the door. Meanwhile, our workforce demographics are rapidly aging. Ten thousand people a day will be turning sixty-five over the next two decades. I’ve seen various predictions, but some research suggests that 27% or more of the workforce will be retiring over the next five years.
What we have is a convergence of all these elements that is imposing itself on the workforce. Disruption is getting worse.
Diana Davis: You've touched on the challenges of aging populations and declining working age populations. How do you think Industry 5.0 will help companies deal with some of those labor shortages?
David Crawley: Industry 5.0 will reduce the need for redundant human activity. For instance, I remember at FMC technology – before Technip bought them – they used to have rooms full of people working on data tabulation.
You certainly wouldn’t have that now with advancements in technology. Now we have technology that can read the printed word, transcribe the document, scan and search documents – all without human intervention.
Industry 5.0 will eliminate jobs, it will also create new jobs, with new skills.
Of course, that comes with other challenges. How do you retrain your existing workers with the skills required for new jobs? Will the workers be willing to be retrained? For instance, if a worker is close to retirement age, will they want to learn an entirely new way of doing things?
Diana Davis, IX Network: What's the best approach for getting the right skills in place?
David Crawley: First, you must understand that there are certain mindsets that need to be in place. With all the uncertainty, are leaders comfortable with ambiguity? It is OK to fail, for instance. This notion is completely contrary to the way most people around the world are trained.
Large corporations are built to scale. In the energy industry if you make a mistake and something fails, it might cost hundreds of thousands of dollars or more! You can see how that leads to a risk aversion to change. You don’t want to experiment and break something because it might cost your organization a lot of money.
What needs to be in place is a culture from the top down that you “fail fast” and “fail cheap.”
When you look at fail fast, fail cheap, you want to engage in a manner that is called systems thinking. No matter how great your solution is, it is going to disrupt something. Sometimes, it is going to disrupt everything.
Therefore, what we want to do is control the disruption. That’s where we get into scenario planning. You need to run through different situations – scenarios – and model the impact.
You need to figure out where potential “death threats” are. These are problems that are serious enough to impede your progress, waste resources and cause organizational wheel spinning. Where will things go wrong?
Digital twinning is one way that you can create simulations so that you can model how different technologies connect, for instance.
Look for the problems. Deal with the hardest ones first. And be prepared to pivot.
There are different methodologies that you can use. There's Agile. There's Design Thinking. There's Deming’s system’s Plan, Do, Study, Act. These are all approaches to building a transition culture of innovation.
Diana Davis: What advice would you give to manufacturing companies on how they can build an effective culture for Industry 5.0?
David Crawley: Companies need to figure out how they model progress, who they are, what their purpose is, and where they want to go.
They also need to know what they are willing to fail at and what they are not willing to do.
Do not try to do everything immediately. You need to prioritize and put together a road map. What is your low hanging fruit? What are the serious problems you must solve? What are the strategic things that will help you build stability for the future?
Understand that some jobs are going to disappear. You need think about which ones will go, and set up a program to educate and train your people to have the opportunities and skills for the next evolution.
You must make sure that the strategy of your business and the company's prosperity drives everything, not technology.
As our workforce retires and young people enter, our workplace cultures are changing. Younger people have a propensity to be excited about technology and the cool things that it does.
That excitement needs to be balanced. You should never buy technology because its “cool” or what the technology promises to do. You should have in place your core strategy and purpose of what you want to accomplish and where your company is.
Are you optimizing the workforce skills? Does this optimization include problem solving and leadership? Are you optimizing your company’s technology skills? Are you empowering your workers?
Finally, leadership needs to be trained on the disciplines of innovation skills. Innovation is something that is meaningfully unique. This issue of innovation is extremely important. Innovation changes the rules on the competition.
The population, the workforce, and businesses need to build their skills to generate and commercialize the ideas of the future. This will be paramount over the next 5 to 10 years.
Interested in Learning More About this Topic?
Equip your workers with the skills of the future. Learn how to navigate transformation, close the digital skills gap and constantly push innovation, productivity and quality at the Connected Worker Manufacturing Summit.
Join over 300 industry leaders on 27-29 June 2022 in London at and learn how to build a connected workforce to improve resilience, agility, and growth in a recovering economy. Learn more about the event here.