Manufacturing Predictions from the Metaverse and Beyond
Add bookmark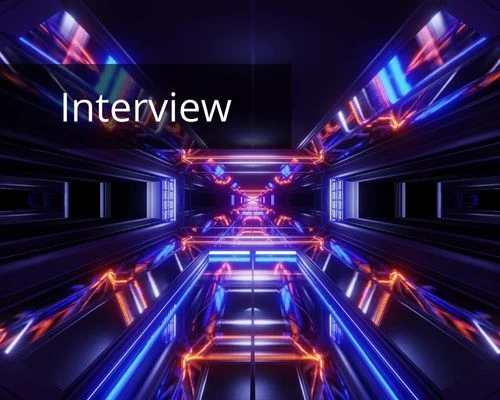
What comes after Industry 4.0? Clearly the answer is Industry 5.0, right?
Not so, according to Jan Burian, Associate Vice President, Head of Manufacturing Insights EMEA at IDC. He says he believes that sustainability will be at the heart of the next industrial revolution, which he calls Green.0.
“Industry for 4.0 was about really creating that cyber-physical environment,” he says. “Integrating the ESG perspective into that will be a game changer.”
In this interview, Burian offers his thoughts on the challenges manufacturers face in the months ahead, predictions on emerging technology and key trends to watch out for, and explains how he thinks sustainability will play into the next industrial revolution.
Diana Davis, Industrial Transformation Network: It has been several years of bad news for manufacturers with ongoing labor shortages and supply chain challenges. What do you think are the big headwinds that manufacturers will be facing as we head into the autumn and the back half of the year? More of the same?
Jan Burian, IDC EMA: It depends on your region.
In the US, the Inflation Reduction Act (IRA) that President Joe Biden recently passed could be a game changer for manufacturing. The IRA aims to support production and reduce dependency on foreign countries, especially in terms of critical components and materials like lithium, nickel, and others.
In both the US and UK, we are seeing reshoring efforts from significant manufacturers like TSMC (Taiwan Semiconductor Manufacturing Company), Intel, Texas Instruments, and Samsung. That should start to help the manufacturing environment within those countries but there will still be ongoing supply chain issues.
When you look at Asia, there are supply chain issues and ongoing labor shortages.
Finally, when we talk about Europe, the market is very fragmented but the war in Ukraine is having a significant impact on manufacturing in the region especially with regards to energy prices. This could worsen as we head into winter and impact manufacturers that rely on high energy inputs – such as glass makers - disproportionately.
Diana Davis, Industrial Transformation Network: Shifting from geopolitics to technology: we spoke earlier this year about how manufacturers can make use of the metaverse. How have things been evolving in that space, say over the last six months since we spoke to earlier this year?
Jan Burian, IDC: Siemens and NVIDIA – both relevant companies in this space - have recently announced an expansion on their partnership to enable the industrial metaverse; they would like to increase the use of AI-driven digital twin technology.
The output would be photorealistic representations of physical assets in the digital twin. This could be embedded in the industrial metaverse, to provide a realistic virtual world. This means you can do plant walk throughs and plant design in a photorealistic virtual world allowing you to see down to the details of the screws.
This is one of the key developments in the past few months, but I caveat this by saying that use cases are still very isolated. For instance, BMW’s Digital Omniverse Factory, Ab InBev’s Digital Brewery, and Hyundai Motors’s Meta-Factory, to name a few. In the future, digital models of real-world manufacturing factories will be linked through the metaverse.
The future really belongs to these islands of use cases being connected, to create a digital representation of the real world based on real-time and realistic data. It should enable users to not just walk through something but also to interact and simulate impacts. Simulation is a crucial capability of this entire effort.
Diana Davis, Industrial Transformation Network: How do you keep the digital representation up-to-date as the physical as the real asset changes?
Jan Burian, IDC: The computing power required will be enormous. It will take effort and be complicated to maintain it just for one factory. But I believe that just like the Internet started small, with a limited number of users and capabilities, I think the industrial metaverse will grow over the next twenty years to become a powerful industrial tool.
Diana Davis, Industrial Transformation Network: What other technologies do you think we should be keeping an eye on?
Jan Burian, IDC: I do not want to talk about the obvious technologies like cloud computing, because they have been discussed a lot over the past few years.
Emerging areas include quantum computing, ultra low latency 5G, and, of course, the industrial metaverse.
Let’s start with quantum computing in manufacturing. Classic computing has a computational wall. Quantum computing can increase the number of factors for more complex analysis, which we believe would be an enabler for development of new products or services for which complex computing power is needed.
For instance, there is talk about responsive organized organic models based on evolving real-time market demand. From an IT perspective, this is a complex computational challenge for which we’d need quantum computing.
In terms of ultra low latency 5G, we are looking at applications for autonomous last mile logistics based on interconnected sensors and ubiquitous IoT. Ultra low latency means that the 5G network will be more reliable; data processing and internet response times will be faster. This will enable new use cases in manufacturing and transportation.
Finally, the metaverse will enable complex, holistic digital twins, as we have already discussed.
Further in the future we are likely to see evolutions of AI that will help to manage and direct our operations – but that is too far off in the future to consider it an emerging technology.
Diana Davis, Industrial Transformation Network: As we approach autumn, any predictions on where we are heading?
Jan Burian, IDC Insights: My organization, IDC Insights, has a number of long-term predictions. We believe that by 2027, the number of physical assets and processes modeled in a digital twin will increase from 5% currently to 60%, resulting in operational performance optimizations.
By 2024, 40% of manufacturers will share data in their ecosystems (partners, customers, suppliers), thereby improving the OEE of their factory operations on average by 10%.
We believe that the future is about sharing the data right with the and not just within a single company but also with the partner’s custom suppliers to help enable performance improvement beyond traditional lean performance improvement activity. This can also help with better supply chain management.
We think that we will see more “citizen developers.” This means that the people in the factories and companies create their own smart customer applications to support their daily business. We expect that by 2025, 60% of organizations will rely on low code platforms and tools to build smart custom applications.
This has the potential to make a significant impact because now workers do not just have to improve processes in isolation, they can easily come up with more robust technology solutions by themselves. It means that the technology tools are no longer dictated by IT or limited by the capabilities of Excel.
Diana Davis, Industrial Transformation Network: One of the things I am starting to hear talk of is industry 5.0. Is this just another buzzword? Are we done with Industry 4.0 already?
Jan Burian, IDC Insights: From my perspective, Industry 5.0 is a marketing term. I have seen definitions of it to mean distributed production, intelligent supply chains, and hyper customization.
If we consider Industry 4.0 - which is based upon the cyber and physical world coming together in the form of robots, automation, digital twins, IoT, etc. – it is clear to see that there is still more room for improvement.
Our research finds that only about 30% of global manufacturers in Europe believe themselves to be mature in Industry 4.0 factory initiatives.
There are some who have built the infrastructure foundation and now they are building the use cases upon that foundation. Other companies have many digital silos – you have a solution for this and a solution for that – that are not connected across the entire company. The benefits come when you can improve processes and leverage the insights from data sharing and contextualization.
So, there is still more work to be done on Industry 4.0.
What happens is that marketers come along, and they feel that Industry 4.0 has been around for a while – it has been about a decade since we first started talking about it – and want to create a buzz around what is next.
But while I think that mass customization and greater integration of artificial intelligence are coming and important evolutions, a colleague of mine, Lorenzo Veronesi, and I have come up with a concept that we believe will be next.
Instead of the shift from Industry 4.0 to 5.0, we believe that will start to see “Industry Green.O.” This is where we start to leverage technologies like cloud computing and IoT for purpose driven results. This is going to be propelled by regulations, but also by the market, investors, and consumers.
Industry for 4.0 was about really creating that cyber-physical environment. Integrating the ESG perspective into that will be a game changer. The next evolution will not be 5.0 – intelligent supply chains and more technology is part of the fourth industrial revolution.
The next evolution will be Green.0. It is a departure from our current way of thinking. It means incorporating new decision-making elements into our operations to support sustainability and new models and approaches. I think Green.O will be game changing.
Interested in learning more about this topic?
If you want to find out more about game changing technologies and approaches to optimize the performance of your people and drastically improve productivity across your operations, then you must attend our Connected Worker Summit.
Taking place November 15-17 in Chicago, the program has been designed to help you understand how to leverage connected worker technologies to improve operational efficiency, training, asset management, quality, and safety. Download the agenda here.