A Closer Look at Qnergy’s Stirling Engine and Methane Abatement Solutions
In conversation with Ory Zik, CEO, and Isaac Garaway, Chief Technology Officer at Qnergy.
Add bookmark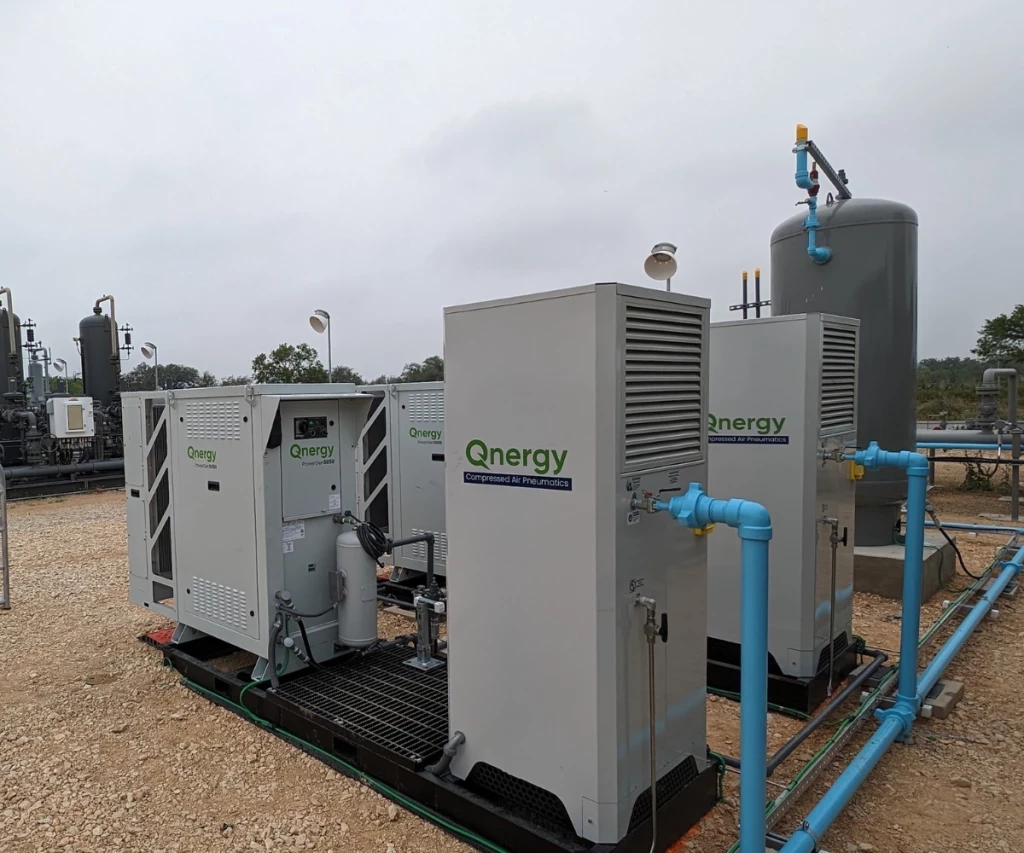
Emissions in the oil and gas industry are largely a result of power and operational limitations, stemming from the way infrastructure and operations were initially established when upstream and midstream locations were first developed. The energy industry, particularly now with the growing need to reduce emissions within natural gas production, faces numerous technological and implementation challenges.
Qnergy was founded on a compelling dual vision: converting otherwise wasted methane into useful energy and providing reliable power anytime, anywhere. They achieve this by transforming waste methane into a source of clean, reliable electricity. In doing so, Qnergy is helping to define a new chapter in the emerging circular economy, while partnering with customers on their ESG goals and journeys to net-zero.
To learn more about Qnergy’s contribution to the methane mitigation landscape in oil and gas and beyond, we spoke with CEO, Ory Zik, and Chief Technology Officer, Isaac Garaway. Ory brings extensive leadership experience in renewable energy and energy efficiency to the conversation, while Isaac offers decades of experience in innovative energy devices, particularly focusing on resonant free-piston Stirling engines.
Read as they share exclusive insights on the challenges and successes in deploying cutting-edge technologies within the industry, the development of the CAP Pico, and how it specifically addresses methane emissions from pneumatic devices.
Maryam Irfan, Industrial Decarbonization Network: Ory, could you share your journey as an entrepreneur and physicist, leading Qnergy’s mission to lower methane emissions, and what inspired you 6to focus your efforts in this area?
Ory Zik: I started my career as a physicist, but early on, I decided that I preferred working on products over writing papers. While I was a PhD student, I was also an environmental activist, so I combined the two interests.
In 2007, I started a solar company called HelioFocus. We were building large solar collectors for conventional power plants, trying to mix gas with solar energy. The venture ended up being commercially successful to an extent, but from an environmental standpoint, it was shocking how much embodied energy and carbon were going into our product. Nobody in the industry at the time was talking about this, which was interesting as a physicist - creating something clean but not knowing how to account for its footprint.
This led me to start a company called Energy Points, focused on environmental accounting. We sold the company in 2015, and in around 2016, the investors of Qnergy invited me to visit. They had a working Stirling engine, which had a long-standing reputation as a promising technology that never materialized into a product. For 200 years, people talked about Stirling engines (a heat engine that converts heat energy into mechanical work), but nobody had built a viable product yet… and that is how I ended up at Qnergy!
Maryam Irfan, Industrial Decarbonization Network: Isaac, as the Chief Technology Officer, can you explain your role within Qnergy and the journey that’s led you here?
Isaac Garaway: As the Chief Technology Officer at Qnergy, my role has been to guide the evolution of our technologies, which originated as remote power solutions, and adapt them into practical solutions that the natural gas industry can use to modernize its operations.
The reality is that while our current technologies are cutting-edge, the technologies that the natural gas industry originally implemented in upstream exploration and production date back to the 1940s, 1950s, and 1960s. These included pneumatic valves and controls, driven by the lack of electrical power and infrastructure at those locations. These solutions are not only inefficient from an emissions standpoint but also costly, as they often involve consuming natural gas for local operations.
Fast forward to now, Qnergy has introduced a suite of remote power technologies that offer natural gas producers’ electricity, compressed air, and advanced controls and communications. My responsibility has been to adapt and apply our technology in ways that allow the natural gas industry to seamlessly transition to modern, clean, and efficient systems.
DOWNLOAD: Special Report: A Look at the 2024 Methane Mitigation Technology Landscape
Maryam Irfan, Industrial Decarbonization Network: How does Qnergy differentiate itself from other solution providers in the methane mitigation space?
Ory Zik: We decided to focus on methane because, from an environmental standpoint, methane is an area where people can have an impact relatively quickly. With my background as an environmentalist, I recognize that abating CO2 is much harder due to the economy's dependence on fossil fuels.
We differentiate ourselves by focusing on what we call distributed methane, whereas most current methane abatement methods involve large, centralized, and very expensive projects. Methane is emitted in a highly distributed manner - think of your garbage can, small dairy farms, and other small sources. Yet, the abatement methods today are centralized. For example, renewable natural gas facilities require large refining operations and connections to natural gas pipelines, and landfill gas-to-energy projects are large-scale facilities that need significant operating landfills.
Qnergy differentiates itself by offering a relatively small generator that can operate remotely, without needing a grid or infrastructure. We can place our solution where methane is emitted, helping us address the infrastructure challenge head-on.
Maryam Irfan, Industrial Decarbonization Network: So, we want to know more about Qnergy’s proprietary Free Piston Stirling Engines (FPSE). What role does it play, and how does it address methane emissions and minimize environmental impact?
Isaac Garaway: A lot of the primary drivers behind the emissions in the natural gas industry today are a result of the industry's need to deploy upstream and midstream solutions without access to electricity. This has led to the use of pneumatically driven systems and controls that didn't account for the availability of electrical power.
The Stirling engine, by definition, is a small conversion device capable of converting raw, unfiltered natural gas directly from the ground into electricity. We’ve introduced a technology that offers continuous, reliable power, essentially providing a 'power plant' on location without the need for traditional infrastructure. Even if you’re 200 miles from the nearest road or 100 miles from the nearest power pole, we can deliver electricity as if you were next door to a power plant.
With this technology, all the solutions needed to control, power, and monitor well pads - including security systems which depend on electricity - can now be deployed. When the natural gas industry realized they could replace pneumatic controls and devices with electrical ones, they also expressed interest in maintaining pneumatic systems while eliminating methane. So, once you have a free-piston Stirling engine providing reliable electricity, you can generate compressed air to replace methane, allowing for a pneumatically driven well pad without the associated emissions. It can transform a highly emissive methane site into a zero-emission site in under an hour.
The free-piston Stirling engine allows producers to rely on an external power source, similar to standby generators used in homes, businesses, hospitals, and hotels. However, unlike typical standby generators, the Stirling engine is built for continuous operation. We have generators that have been running for over 50,000 continuous hours on well pads across North America, Central America and South America.
Maryam Irfan, Industrial Decarbonization Network: Can you explain how the Stirling engine’s design contributes to minimal maintenance and reduced emissions?
Isaac Garaway: The key to success for natural gas producers is moving away from methane and transitioning to electricity and compressed air. The strength of the free-piston Stirling engine lies not only in its continuous operation but also in its reliability, which allows producers to deploy it and essentially walk away, confident that their assets will continue to operate as before.
The Stirling engine takes a small fraction of the natural gas coming out of the ground, oxidizes it, and converts it into CO2 and heat through a process that uses a high-temperature radiant matrix premixed burner. The process works by absorbing heat into the hot end of the engine, causing an inert gas inside the engine to expand. This gas, typically helium, is sealed in a hermetically closed cylinder. As the gas expands due to the heat, it moves a piston, which then produces electricity. As long as there is heat, it can produce electricity continuously, ensuring that the well pad operates reliably without the need for constant maintenance.
Maryam Irfan, Industrial Decarbonization Network: What challenges have you faced in bringing the free-piston Stirling engine to market, and how have you overcome them?
Ory Zik: The Stirling engine has been in development for about 25 years, starting with a project funded by NASA, which made it notoriously expensive. One of the key challenges was figuring out how to make something developed for space, and thus very costly, affordable for everyone on Earth. This required simplifying the material selection and design.
Secondly, as a small company with unique technology, we needed to develop our own supply base of OEM parts, as there’s hardly anything we can borrow from others.
Lastly, developing and stabilizing the technology! It takes a lot of time because every little detail - every little spring and piston – requires careful development.
LISTEN: Episode 12: Navigating US Methane Rules with the American Petroleum Institute (API)
Maryam Irfan, Industrial Decarbonization Network: A press release published on 2 May, 2024 revealed that Weber Country and Qnergy kicked off a pilot program to convert the methane emitted from the closed landfill into on-site electricity. How does this reflect Qnergy’s approach to tackling methane emissions, and what are the key takeaways from this initiative?
Ory Zik: As a distributed energy company, we started by targeting the three main methane-emitting sectors: oil and gas, waste, and agriculture.
The Utah project is one of our first commercial pilots in the landfill and waste space, and now we're developing and expanding into agriculture. We focused on closed landfills because of the distributed nature of methane emissions. The US has about 1,500 active landfills and more than 10,000 closed landfills. Closed landfills are more reliable, both environmentally and financially, for their owners, but they are not typically considered an asset.
What we've learned along the way is that we have amazing partners. The community in Weber County, Utah, has given us access to the landfills, which are just a 10-minute drive from the factory. We have three closed landfill projects that are active, with one already in operation. When you consider their proximity to the factory, you realize just how big the market potential is. There are likely more than 10,000 landfills in the United States alone. What we do is provide the equipment for free, generate revenue from carbon credits, and share these revenues with the community - the landfill owners - who need these resources.
Maryam Irfan, Industrial Decarbonization Network: Earlier this year, Qnergy announced the launch of the solar-powered Compressed Air Pneumatics (CAP), which is ideal for low air requirements and remote applications. Can you explain how it specifically addresses methane emissions from pneumatic devices?
Ory Zik: Typically, oil and gas operations don't have electricity on site. Instead, they use the pressure of the gas that comes out of the ground when they drill as a source of power. This pressure is needed to perform various activities on the site, such as separating gas from water, oil, or mud, or directing the gas to different pipes.
To manage these activities, the industry developed a network of pneumatic valves, which are simple, reliable, and convenient. However, there's one challenge: whenever a valve changes position from closed to open or open to closed, it vents a little bit of methane. While each venting might seem minor, there are about a million valves in the US, so a little bit multiplied by a million becomes substantial - equivalent to the emissions of approximately 10-20 million cars.
Most of our compressed air product line was previously designed for higher airflow, large, and active well pad applications. And, while working with key multinational corporations, we identified a need to provide a low airflow, lower cost solution.
The US has around 50,000 large wells and about 500,000 smaller ones, so the industry needed a solution that was low-cost and accessible to all operators, large, small, operational, or closed. This need drove the development of the CAP Pico, which is a low-cost solution designed for the long-tail of well distribution, addressing those wells that emit small amounts of methane but still require a very reliable solution.
Maryam Irfan, Industrial Decarbonization Network: Isaac, can you share the technical specifics of the CAP Pico?
Isaac Garaway: The free-piston Stirling engine has been a tremendous asset in the natural gas industry, providing close to 6,000 watts of clean, dispatchable, and reliable power 24/7, with tens of thousands of hours of operation without maintenance.
Most emissions within the natural gas industry come from small well pads and low-value assets, a classic case of 'death by a thousand cuts.' In North America alone, there are about 400,000 wells, with the majority being single wells spread across the continent. These wells are low-value, and while each emits only a small amount of methane, the cumulative effect is significant.
High-value well pads are more economically viable for deploying a free-piston Stirling engine generator with compressed air. These sites can easily justify converting from methane-driven to electrically and air-driven systems, making it a simple and financially sound decision. However, the hundreds of thousands of single-well pads with low production cannot afford the infrastructure required for such a high-value package. That's where the CAP Pico comes in.
The CAP Pico is specifically designed for small, low-value, single-well pads with minimal air and electricity demands. Despite its smaller scale, it still provides the reliability and continuous power supply our customers expect, along with the same alarms, notifications, and remote capabilities.
Uniquely, it runs on solar power, our first product that doesn't incorporate the Stirling engine. It can function as a standalone solar-powered unit, or hybridize with other power sources. Most importantly, it's cost-effective, allowing operators to continue their efforts in emissions reduction even on their low-value well pads.
READ: 6 Cutting-Edge Technologies to Help Achieve Net-Zero Emissions
Maryam Irfan, Industrial Decarbonization Network: What are the critical technical challenges you encounter when developing new methane mitigation solutions, and how do you address them?
Isaac Garaway: As the Chief Technology Officer, my focus is on finding solutions to real industry problems. While new regulations and laws are starting to mandate emissions reductions, natural gas is still being produced today without any measures.
The best way to encourage the industry to move toward an electric or compressed air-based economy is to provide solutions that don't create additional challenges. We are actively working on a technology suite that can address nearly any methane emission issue impacting the industry, including well venting, casing vents, and tank vents.
So, the technology exists and works, but the real challenge is packaging it in a way that’s seamless and painless for the user. It must be so straightforward that the operator can simply push a button, walk away, and know that it will work continuously.
As we deploy more products into other challenging areas within the industry, we're working hard to make the process as smooth as possible. This means going out to well pads, working with operators, and observing their current processes. We want to ensure that when we deploy a solution, it not only eliminates emissions but also improves the operator's experience.
Maryam Irfan, Industrial Decarbonization Network: What emerging technologies or trends do you foresee having the most significant impact on methane mitigation space in the next 5-10 years?
Isaac Garaway: Over the next year, we'll likely see the industry resolving highly centralized leaks, whether at midstream or upstream locations. However, the real challenge lies in the fact that the majority of methane emissions are decentralized. There are hundreds of thousands of these leaks, all very small, occurring 24/7, throughout the network.
It’s not just accidental leaks, some leaks are an inherent part of the process - whether it’s a compressor seal, a tank, or a valve, they may leak briefly, but they leak, nonetheless. The real challenge for the industry is developing decentralized solutions for these emissions.
Currently, the industry is heavily focused on monitoring and detection, whether through drones, sensors, cameras, or infrared technology, and the reason is simple: many of these leaks are not immediately detectable. However, the problem is the lack of solutions addressing those leaks.
I believe this will be the industry’s biggest technology driver in tackling methane emissions over the next five years.
Maryam Irfan, Industrial Decarbonization Network: Lastly, Ory, how do you see the market for methane mitigation evolving in the next five years?
Ory Zik: Methane, as you know, is much simpler to abate than CO2. Since it’s a fuel with value, abating it in a way that can also generate revenue is advantageous. Over the next five years, we will likely see a trend where the easier-to-abate methane sources are addressed first, like what we're observing with renewable natural gas and landfill gas-to-energy projects.
Regardless of whether it takes five or ten years, humanity ultimately needs to abate all methane sources. There's no reason to vent methane, especially if climate change is a pressing issue. In the coming five years, the low-hanging fruit will likely be addressed first, after which efforts will shift to tackling the more challenging methane sources in the oil and gas sector and other industries.
READ: Attendee Insights on the Biggest Methane Mitigation Challenges and Investment Priorities
Interested in learning more?
Join over 250 of your peers in Houston this December 3-5, 2024, at our upcoming Methane Mitigation America Summit. This year's Summit will offer exclusive insights and knowledge on balancing technological innovation with operational efficiency, particularly in the context of an evolving regulatory landscape. Download the agenda for more information.