How Robots and Automation Enhance Operations at Cameco
Add bookmark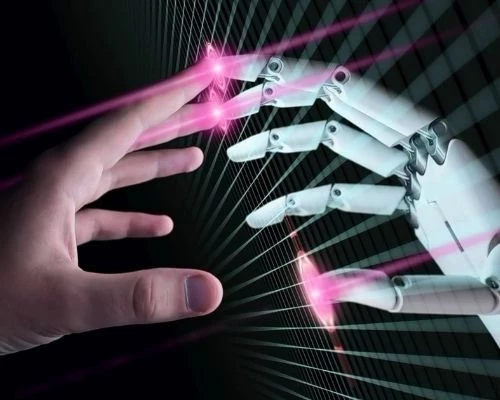
Cameco is a Canadian uranium mining and processing company that is making its operations safer and more efficient through a combination of robots, artificial intelligence, and advanced process control.
You can’t have technological success, however, without a relentless focus on people and process too, says Andrew Thorne, Vice President of Mining and Operational Excellence at Cameco.
“You need to put just as much effort into the people and the process as you do the technology,” he observes. “If you don't, you won't extract the full value of that technology investment.”
Thorne looks after the company’s mining operations in northern Saskatchewan. In this interview he discusses how his company is leveraging robotics and automating processes to make operations safer and more efficient, lessons learned about digital transformation, and building the skills of the future.
Diana Davis, IX Network: In the past few years, our world has turned upside down and back again. It feels like the disruption just keeps on coming. How have the external disruptions of the past few years affected your operations at Cameco?
Andrew Thorne, Cameco: The effects of COVID have been significant for us as a company.
We operate fly-in, fly-out operations in northern Saskatchewan. Our workers work and live together for two weeks at a time. That creates additional complications as they’re not just coming to work for the day and going home at night.
For the past couple of years, we have had to continue our uranium mining operations, but we've also had to run COVID isolation units.
While provincial regulations around isolation have recently dropped, at the height of COVID people had to isolate for 14 days after symptoms. If a worker became ill on site, they needed to go into isolation. They couldn’t go home; they were stuck at camp.
For the last two years, we have been managing those isolations. We have had to feed people, make sure they had the appropriate medication and received the appropriate medical care.
COVID, as you can imagine, has been incredibly challenging for us.
Diana Davis, IX Network: It sounds like you've had to run an entirely new operation, on top of your regular mining operations.
Andy Thorne, Cameco: That’s right. The other challenge that has posed operationally is the effect of high absenteeism.
If our workers get COVID at home on their two weeks off, they're not able to come back to work. We had such elevated levels of absenteeism at times that it resulted in us shutting down mining activities because we didn’t have enough employees on site to produce safely. Our culture at Cameco is safety always trumps production.
Diana Davis, IX Network: How have you been leveraging digital technologies to respond to these challenges and drive operational excellence?
Andrew Thorne, Cameco: We, like many mining companies, have a strong focus on digital transformation right now. In the mining industry there's been a recognition that the application of digital technologies has the potential to make our sites safer, improve our environmental performance, reduce our costs and/or improve our revenues through increased production throughput.
We have a program that we call AMPED-UP. It stands for Advanced Mining and Processing through Efficiency and Digitization - Uranium Project.
We have a portfolio of about 50 projects that touch all aspects of digital transformation and we're applying those to our operations as we speak.
We're about three years into our digital transformation journey. We're doing projects around automation, robotics, predictive maintenance, data analytics, machine learning, and AI.
Diana Davis, IX Network: What have you been using the technologies to do? Could you give me a specific example?
Andrew Thorne, Cameco: We have a couple of large projects around automation.
For instance, we package uranium in drums and, historically, it has been a very manual task.
We would fill the drums and then label them – all manually. A worker would need to manually put lids on the drums and then bolt on a ring on to keep the lid in place.
Now, we’re using a robotic arm to carry out this procedure.
We're also putting a lot of focus on advanced process control. We have a big project where we’re looking to reduce process variability using computers to make decisions on how to optimize a process.
Historically, we would have an operator in a control room tweaking knobs and dials to change levels of reagent dosage. Now we're moving to a place where we're using algorithms to make some of those decisions. That allows us to eliminate waste and get more efficient with our reagents.
Diana Davis, IX Network: I imagine that the first example you shared also makes your operations safer, for instance, with robots reducing contact between workers and uranium?
Andrew Thorne, Cameco: In any industrial plant when you have humans interacting with equipment, chemicals or hazardous materials there are inherent risks. One of the controls to reduce risk is reducing the frequency of interaction that a human has with that equipment or material.
Specifically with uranium, it is a material that you absolutely want to make sure you manage appropriately. Any time we can reduce the operator interaction with uranium it reduces the risks associated with producing our product.
Diana Davis, IX Network: On the flip side, what have been some of the bigger challenges of integrating technologies like these into your operations?
Andrew Thorne, Cameco: That’s a good question. I’ll give you a specific example.
We have a strong focus on mobility. We’ve been very reliant on paper-based systems, and we made the decision that our operations will become as near paperless as we can get.
For example, maintenance work orders have always been paper-based. We would print out the work orders and then the work orders would be handed out by the supervisor to the tradespeople. We've now eliminated that process. All tradespeople are being issued with iPads; we dispatch work orders electronically.
This sounds simple, but not everybody is comfortable with technology. This has meant that we’ve had to focus on change management, reskilling, and marrying the technology with the culture and the people.
When you’re driving digital transformation, you need to really think about three things: people, process, and technology.
We learned early on that it's very easy to get excited about the technology and forget about the people and the process.
You need to put just as much effort into the people and the process as you do the technology. If you don't, you won't extract the full value of that technology investment.
Diana Davis, IX Network: I hear a lot of people say that the technology part was easy. It was the behaviors and the culture change that was the hard part.
Andrew Thorne, Cameco: One of the things we’ve struggled with is the latency of data transfers. Humans aren't particularly patient. Nobody wants to wait 30 seconds for the work order data to download to the iPad. If that's the kind of customer experience that they're getting, they lose patience and give up on the technology.
That’s why ensuring that the operators have a positive customer experience with the technology and providing encouragement to use it has been an important part of the change management piece.
Diana Davis, IX Network: You also mentioned reskilling. How have some of these technological changes impacted your people and the skills and capabilities that that you need in your operations?
Andrew Thorne, Cameco: We operate our mines in northern Saskatchewan. We're very proud as a company to say that more than 50% of our workers come from the northern Indigenous communities in which our facilities operate.
The challenge is that those northern communities have limited access to education and skills development opportunities. In most cases any upskilling that we need to do with people from those communities, we need to do ourselves. That's a commitment that Cameco has made to the north.
We've worked very closely with leaders in the north to develop our own online training program. We’ve created a suite of 15 online training courses that residents of Northern Saskatchewan can access from the north and work through at their own pace via computer-based training.
The courses include modules on health and safety, digitization, robotics, and data analytics. We’re investing heavily in trying to raise the digital acumen of our workers.
Diana Davis, IX Network: We touched on the importance of not neglecting your people in the digital transformation piece. Are there other key lessons learned from the past few years?
Andrew Thorne, Cameco: Finding that balance between people, process and technology is key, but I think that other lesson is that you need to be really conscious of change overload.
You can spend a lot of money very quickly on these technologies and there are plenty of people out there that want to sell them to you. You don’t want to move onto the next thing too quickly before you’ve got real adoption of your first technology or software.
The other lesson for us is to make sure that the business process is efficient and effective before you go anywhere near digital tools. There’s no point digitizing an inefficient process.
You need to have the discipline to go back to the tried and tested tools like process mapping, lean, lean tools, value stream mapping, etc.
I think too many companies think the digital solution is a silver bullet. It isn't. You must do the hard work to understand your process and identify the waste in it. You shouldn’t even think about digitizing a process until you’ve optimized it.
Diana Davis, IX Network: It’s interesting that you mention Lean tools. Do you think tools like Lean and Six Sigma are still relevant in today’s digital world?
Andrew Thorne, Cameco: Absolutely. I think they're crucial and critical to the success of any digital transformation. We're very focused on Lean at Cameco. We have over 350 green belts in the company and we're absolutely relying on those tools and techniques that we've historically taught our employees.
I think tools like Value Stream Mapping, 5 Whys, and Root Cause Analysis are foundational for any successful digital transformation journey.
If you don't have solid, robust manual processes, then you're wasting your money to digitize poor process.
Diana Davis, IX Network: What's your focus for your operations in in the year ahead?
Andrew Thorne: The uranium markets have gone through tough times in the past decade following Fukushima, the Japanese nuclear plant that failed following an earthquake last decade. But we're now seeing renewed interest in nuclear as the world seeks viable ways to reduce carbon emissions.
As a result, we have just announced the restart of our Key Lake and McArthur River facilities. Right now, we're in the process of getting those facilities ready to restart. We are hiring and we've been using the down time to modernize the facilities using digital technology.
The next year for us is about creating the environment where we are ready to supply a market that's getting very hungry for uranium.
Interested in learning more about this topic?
Andrew Thorne will be speaking at our upcoming Operational Excellence Week Canada taking place October 17-20, 2022 in Toronto. Hear more about how your peers are accelerating digital transformation, operationalizing sustainability, improving supply chain agility and boosting productivity.
Join over 200 of industry professionals and over 30 world class transformation thought leaders this October. Find out more here.