Tackling Europe's Manufacturing Labor Shortage
Add bookmark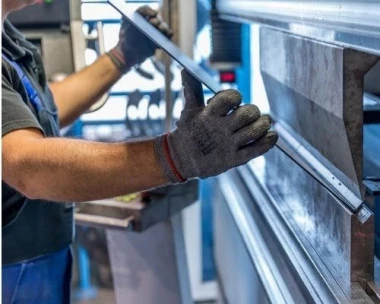
3 ways Connected Worker technology can help European manufacturers train, retain and upskill the next generation of workers.
Last fall we wrote an article that looked at how and why US manufacturers are struggling to recruit and retain workers.
But the problem is not limited to American manufacturers. In 2019, according to Eurofound, 39% of European manufacturing companies reported that their production was limited by labor shortages.
Those numbers are likely to be worse now, compounded by the effects of Covid and changing demographics.
In the UK, for instance, manufacturing job vacancies are 30% higher than their pre-pandemic peak, according to Deloitte. Another report, published in 2020, found that British manufacturers were experiencing the worst shortage of skilled labour in over 30 years.
French tire company Michelin, meanwhile, reported that its 2021 financial results were impacted by labor shortages which meant it was unable to fully meet “robust customer demand,” according to the European Rubber Journal.
“Workers you’ve depended on for decades are leaving the workforce in record numbers. And despite higher wages and other incentives, replacements are difficult to find,” said Jordan Konst, Global Automotive and Tire Industry Consultant at Rockwell Automation, quoted by Rubber Journal.
That trend is part of a wider “graying” of European populations. As EU populations get older and baby boomers retire, there are not enough young people entering the workforce to replace them.
A UN analysis predicts that Europe will lose 95 million workers between 2015 and 2050.
A McKinsey future of work in Europe study, meanwhile, predicts that by 2030 with the continent will have already lost 13.5 million working age people. Germany - Europe’s manufacturing heartland - will be among the hardest hit with 4 million fewer working age people.
These demographic changes – along with other large-scale trends such as emigration from Eastern to Western Europe and the fall out from Brexit - are having a profound effect on European manufacturers.
Despite advances in automation, robots and artificial intelligence, human workers are still the backbone of manufacturing operations. They troubleshoot the machines. They work creatively to identify and fix problems on the line as they arise. They decide what parts of the manufacturing process to automate and how. They program and repair the robots. They decide how to innovate and change to better meet market demand.
What do you do when you don’t have enough people to get the work done?
Short term, you may need to curtail production. In the long term, however, failing to meet customer demand is not a winning strategy for a sustainable business. Manufacturers must address labor shortages through increased productivity, automation and new digital strategies to attract, train and retain new workers.
That’s one of the reasons that many manufacturers are turning to Connected Worker technology – a category of applications that includes wearables, virtual reality, and mobile apps. The technology connects frontline workers with the resources and information that they need to get the job done safely and efficiently.
Examples of Connected Worker technology include digital work procedures, explanatory videos and wearable technology that helps guide workers. Proponents say it can improve everything from training through to asset management, quality and safety.
Here are three ways that European manufacturers can use Connected Worker technology to address labor shortages and prepare the future workforce:
#1: Attract, engage & retain the next generation of European manufacturing workers
A 2021 survey of companies in the UK and Ireland, found that nearly half (49%) of young people planned to quit their job in the next year.
While not manufacturing specific, the report highlights the challenges of retaining young workers, whose expectations may be different from older generations.
This younger, digital generation is the future of the workforce. Not only are they less likely to stick around long term but they’ve grown up with hand-held, connected devices that run everything from their errands to their social lives.
A manual work environment that relies heavily on pen and paper just doesn’t cut it for them.
“I think that it is extremely important to show to our workers when they’re on site that that we have modern tools for them and that we’re not asking them to work with just a pen and paper and write the same information over and over again,” says Eric Duchesne, Senior Vice President, Manufacturing & Projects at TOTAL Energies in an interview with IX Network's sister publication, Oil and Gas IQ. “[…] It’s not motivating for workers to come to work with tools they perceive to be inferior to what they have in their personal lives.”
Connected Worker technology helps bridge the generational gap and engage the future workforce on their terms making it more likely that your new workers stick around longer.
#2: Replace the loss of tribal knowledge by training in the flow of work
No longer can you expect to rely on the slow processes of knowledge accumulated over years. Tribal knowledge is slow to develop but easy to lose as older, experienced workers retire and younger workers job hop more readily.
The changing work habits of young people and the impacts of COVID means that the industrial workforce has become more spread out and less experienced. Manufacturers must accelerate training to help less experienced workers quickly build their knowledge and capabilities.
The challenge with the traditional way of training is that new recruits usually get too much information thrown at them in a classroom. The result is information overload and much of the knowledge is forgotten as soon as they leave the classroom.
Connected Worker technology gives workers the resources and information they need in the flow of work, which reduces frustration and errors. This ‘learning by doing’ approach ensures better knowledge retention too.
Virtual reality can also help by simulating experiences before the worker encounters the real situation. This is especially useful for jobs that are dangerous (such as working at height), rare (an emergency situation) or difficult to practice in the production environment.
Connected Worker technology has the added benefit of systematizing the capturing the accumulated, tribal knowledge of your more experienced employees. By capturing this information in digital form, Connected Worker technology makes it available for the next generation of your workforce.
#3: Enhances productivity by putting digital tools in the hands of all employees
Getting the wrong information – or having to wait for it- tops the list of reasons for lost productivity for manual workers, according to a 2018 Deloitte survey. Over a third of manual workers said that difficulty accessing the right information were among the top three reasons that they lost productivity during the day.
Connected Worker technology addresses this by giving your employees the right information at the right time so they can make smart decisions. By eliminating the need to manually search for information and allowing shop floor workers to tap into the expertise of their colleagues, connected worker platforms enables workers to quickly get the information they need to take appropriate actions.
Conclusion
Labor shortages look set to be an enduring feature of the decades ahead for European manufacturers. Tools that get new employees up to speed quickly, give them the information they need to be productive and effective quickly, and that foster a sense of community will be critical to recruiting and retaining the next generation of workers.
Interested in Learning More?
As COVID-19 restrictions ease and the manufacturing industry rebounds, industrial employers face an urgent imperative to prepare for the future of work. Learning how to navigate transformation, closing the digital skills gap, accounting for supply chain disruption, and constantly pushing innovation, productivity and quality must be among the top priorities for organisations looking to thrive.
Join over 200 industry leaders on 27-29 June 2022 in London and learn how to build a connected workforce to improve resilience, agility and growth in a recovering economy. Find out more about the event here.