6 Key Takeaways for Connected Manufacturing Work
Add bookmark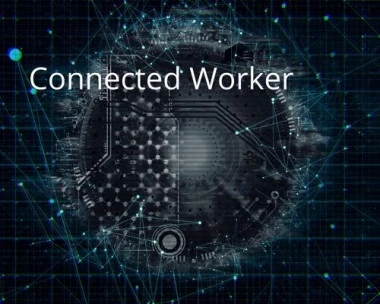
As manufacturing companies seek to drive operational efficiencies, improve quality, and quickly onboard and upskill new recruits, many are turning to a category of software applications that connect workers to the information and resources they need.
Connected Worker technology is a class of software that enables workers to be more effective by harnessing the power of artificial intelligence, cloud computing, mobility, IIOT, wearables and AR/VR to connect and guide them in the flow of work.
A maintenance technician, for instance, can access equipment guides via connected glasses, which allows them to access critical resources in the flow of work, while keeping their hands free.
Clearly, Connected Work promises enormous benefits for the companies that harness it.
However, as Daniel Grobe, Co-founder and CCO at Operations1 pointed out in his presentation at our recent Connected Manufacturing Worker conference, the reality of digital transformation in many manufacturing organizations today amounts to no more than PDFs on tablets and large screens.
At the conference, attendees from major manufacturing organizations shared their insights and experience in what it takes to harness digital technology and drive real business benefits.
Here are a few of the key takeaways:
Takeaway #1: Every company's digital journey is different
Each company has its own culture and starting point. You can’t just look at what another company has implemented and copy it. You need to find the path that works for your company.
Takeaway #2”: Don’t get lost in the technical details
The temptation is to get very excited about a specific technology and run away with it. Rather than starting from a ‘technology first’ perspective you need to focus on the strategy and the value that technology will bring to the organization and the shopfloor.
Takeaway #3: Reduce complexity
Systems must be easy to learn and use. People will avoid using complicated systems. One solution that does multiple things is better than multiple specialist systems, for instance, as it reduces the learning curve and the need to swap between systems. Creating intuitive workflows is key.
Takeaway #4: Get pull, not push
A surefire way to fail is to impose a solution on a plant that doesn’t want it. It’s better to wait until sites are asking for these solutions rather than imposing it on them. Work with the early adopters first to prove value and other sites will want in eventually.
Takeaway #5: Take small steps rather than go for the big bang
It’s better to make smaller, incremental improvements and deliver them then to aim for everything. You can start with a Minimum Viable Product (MVP) and roll it out to start getting benefits right away. As one of the panelists pointed out during a discussion: “Rather than trying to find the perfect journey, sometimes you just need to start moving.”
Takeaway #6: Engage the shopfloor early on
Too many digital transformation projects fail at the final hurdle: user adoption. You need to answer the question for the operator, ‘what’s in it for me?’ to make sure that any solution brings them benefit.
Technology projects are also often met with fears from workers that their jobs will be made redundant. Break down those fears by making sure that your introduction of new technology does not equate to workforce reduction.
What do you think? Where you at the conference? What were your takeaways?
Interested in learning more about this topic?
Join over 200 industry leaders on November 15-17, 2022 at our Connected Worker conference in Chicago and learn how to build a connected workforce to improve resilience, agility and growth in a recovering economy. Download the agenda here.