Interview with Sun Chemicals: Industrial Decarbonization Requires an Ecosystem
Interview with Nikola Juhasz, Global Technical Director of Sustainability at Sun Chemicals
Add bookmark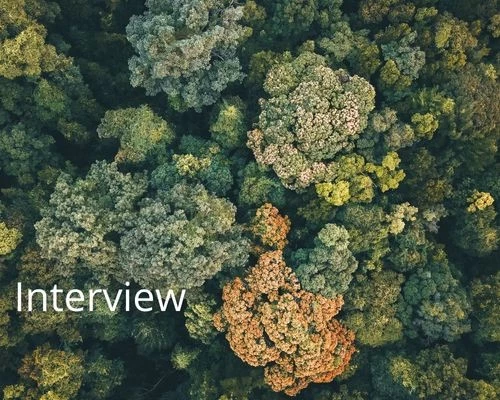
Decarbonizing the industrial sector, which includes chemical, cement, steel and others, is not an easy feat. The materials and processes that go into these industries often require high levels of heat, which is hard to power from renewable energy sources or they produce CO2 as part of the production processes.
Reducing carbon emissions in these foundational industries is going to require a complex interplay of innovative approaches, technologies, partnerships and thinking.
“Industrial decarbonization is not going to happen from one player alone,” observes Nikola Juhasz, Global Technical Director of Sustainability at Sun Chemical. “It will really take collaboration across the entire supply and value chain.”
In this interview, Juhasz discusses how Sun Chemical has been tackling the challenge of reducing scope 3 carbon emissions, explains why sustainability requires a more circular approach and offers her perspectives on the role of America’s industrial sector in the drive to net zero.
Diana Davis, IX Network: Industrial decarbonization is high on President Joe Biden's agenda. How is that affecting your business?
Nikola Juhasz, Sun Chemical: Decarbonization is one element of sustainability. At Sun Chemical, we have been focused on sustainability for many years. We recently issued our twelfth annual sustainability report, which demonstrates our long-term commitment to support new products and services that help customers deliver on their eco-efficiency goals.
Of course, as the pressure increases, decarbonization is receiving heightened attention from a greater number of participants in the industry. For us, we’ve been on the journey to reduce our carbon emissions for a long time.
No company can achieve success in isolation, so having industry players work together to reduce emissions is a positive thing. The grants and funding that are now available for our collective work to enable these types of initiatives is also a positive development.
READ: The 4 Pathways to Industrial Decarbonization
Diana Davis, IX Network: Can you give an example of how you're approaching decarbonization?
Nikola Juhasz, Sun Chemical: Sure. I’d first like to take a step back and reflect on how we approach sustainability at Sun Chemical. Everybody's got their own version of the classic reduce, reuse, recycle and renew.
At Sun Chemical, we tend to think about sustainability in terms of five buckets. These are reuse, reduce, renew, recycle and redesign. We apply that same approach to our product and service developments, but also to what we're doing operationally.
When we're talking about industrial decarbonization, we often focus on what we’re doing in our operational facilities.
When we think about reuse, for instance, we're talking about recovering solvent streams within our processes and trying to reuse them multiple times. Or recovering energy from some waste materials so that they are re-used.
When we talk about the reduce bucket, there are many energy reduction initiatives underway in our operating facilities, and we've made discrete steps to reduce energy use and the associated carbon emissions that come along with those over the years, on a path to net carbon zero by 2050.
We're also moving towards more renewable sources of energy. We’re evaluating renewable electricity and different types of renewable fuels that we can use to power our operating facilities. We have solar arrays in place in a few locations that provide a substantial portion of the electricity needed by those facilities, and we put the excess back onto the grid.
Recycling is about recovering streams and reusing them within our facilities. We also have some examples of taking waste streams from other processes that are local to some of our facilities and using those as input streams for our production.
Redesign has to do with things like bringing in automation or reimagining production campaigns for improved efficiency and lower energy consumption.
This should give you a sense of what we're doing to reduce our operational footprint and scope 1 and 2 emissions.
Diana Davis, IX Network: Can you tell me more about how you recycle waste as an input for your own production processes?
Nikola Juhasz, Sun Chemical: In one of our pigment production locations there is a nearby steel processing facility that produces a waste stream that we can use as a feedstock for our manufacturing process.
Steel pickling refers to a treatment that removes impurities, rust and scale from the surface of steel metal. To remove these contaminants, the steel is dipped into a vat of what is called “pickle liquor”.
The spent pickle liquor then becomes a feed stream in our production of iron oxide pigments for cosmetic applications.
Instead of having to landfill or otherwise treat this waste material, we can bring it in as a feedstock to produce a high-value product.
READ: SPECIAL REPORT: How Canada’s Industrial Sector is Powering Net Zero
Diana Davis, IX Network: What are the biggest decarbonization challenges in your industry?
Nikola Juhasz, Sun Chemical: We are the largest global supplier of pigments and we've recently completed an acquisition of the former BASF color and effects business. Pigment production is a fairly energy intensive process.
Our other high-volume business is printing inks, coatings, and adhesives, which have important applications in packaging products, and are an especially visible source of waste in the environment.
Our operations are only a small portion of our overall carbon emission footprint, however. Our biggest challenge is to reduce our scope 3 emissions, which are coming from our upstream supplier base and from the downstream impact of our products.
While we know that a crucial element of our sustainability journey is making sure that our own house is in order, we are also mindful of the fact that much of the carbon footprint that we represent comes from the materials that we use external to our own operations. So, we are working with our suppliers to find alternative materials and more efficient ways to produce them.
We’re also looking at the disposition of our materials downstream. Can we design them so that they can be more easily recycled if we're putting them onto a package, for example? Do they enable the package to go through a recycling process more easily? Can we help eliminate film layers in packaging by replacing them with coatings for overall light weighting? Can we provide products that help packages to be more readily composted? That helps us to reduce the overall carbon footprint within our market.
We’re designing our products so that the downstream operations are also more efficient and less carbon intensive. This means using more renewably sourced materials responsibly.
Renewably sourced materials have some biogenic component that can help to sequester CO2; those plant-based materials are consuming CO2 versus putting it out into the environment.
The more that we can work upstream to help define and design those raw material inputs that we'd like to see in our products, the more that the industry overall becomes decarbonized.
Diana Davis, IX Network: What would you say is the biggest challenge to embed these more sustainable solutions in your business?
Nikola Juhasz, Sun Chemical: There are a couple of challenges.
The big established petrochemical players who represent an important part of our current supplier base are undergoing a transition to become more sustainable and to offer different types of raw materials. Many are switching to more renewably sourced feedstocks in their processes, for instance.
But that's a transition that doesn't happen overnight or all at once.
So, mass-balancing approaches become important, which require carefully documenting the steps that have been taken, and properly associating them with a portion of the raw materials.
There can also be challenges in terms of swapping in some of those more sustainable, less carbon intensive raw materials. They may not necessarily be drop-ins. We must redesign our products using those materials and make sure that we're delivering the same performance.
There's often a cost element that must be managed as well.
Sometimes the raw materials that come with more favorable sustainability characteristics will not be available in large volumes and therefore the costs will be higher. That means that we need to manage how we position our products in the market.
Additionally, it is important that we validate that the new materials and products we are bringing to the market deliver the environmental benefits that we'd like to see, through detailed and credible life cycle assessments. That's a process that we are undertaking with our supplier partners, which means making sure that we're all talking the same language, exchanging information and agreeing on the input and output data, as the outputs need to feed the downstream models of our customers and their customers as well. This is a complex process, still in its relative infancy, and poses another challenge.
Diana Davis, IX Network: What are your key lessons learned on embedding sustainability within your business?
Nikola Juhasz, Sun Chemical: One of the major lessons is the unavoidable need for collaboration up and down and across the value chain. In the traditional model, everybody operated in their space and thought about the immediate upstream suppliers and the immediate downstream customers. But we didn’t necessarily reach further backward or forward.
We now need to understand, how was the material sourced? What are the carbon implications of that source? And what happens with the final disposition of the product? We need to have more contact with the waste management community to understand their challenges and design for them.
This means a more sustainable and more circular approach. When we have a linear economy, we could very nicely just think about our position. In a circular economy, you can't do that anymore. You really have to work with all the players along the line.
Industrial decarbonization is not going to happen from one player alone. It will really take collaboration across the entire supply and value chain.
Diana Davis, IX Network: It sounds like companies need to operate more like an ecosystem? Business imitating nature?
Nikola Juhasz, Sun Chemical: That's absolutely it. I think it’s a nice analogy that our industrial ecosystems should simulate our environmental ecosystems.
Diana Davis, IX Network: What role do you think America's industrial sector, both nationally and globally, needs to play in this push to net zero?
Nikola Juhasz, Sun Chemical: Statistics show that Americans are one of the largest generators of waste and emissions. We have often relied on the rest of the world to deal with some of the outputs of our activities. We have a vital role to play in showing leadership in this area and encouraging others to participate. We can't achieve what we need globally without the largest economies participating and taking leadership.
Interested in Learning More About this Topic?
Nikola Johasz will be speaking at our upcoming Decarbonizing America’s Industrial Sector conference taking place next week in Palm Springs September 13-15, 2022. Join over 200 of your industry peers as they advance clean manufacturing and help reinvigorate America's industrial sector.