How Culture Drives Sustainability at Monin
Add bookmark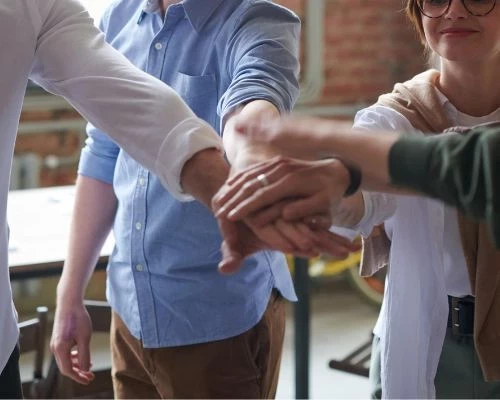
As leading manufacturers seek to reduce their environmental impact and lower carbon emissions, it can be easy to get caught up in discussions of technology and reengineering processes and energy efficiency.
However, there’s an essential element for sustainability that is easy to overlook: company culture.
Monin is a global manufacturer of syrups, sauces, and flavorings. If you’ve had a vanilla flavored latte, chances are good that you’ve consumed one of their products.
The company has committed to reducing its environmental impact by minimizing its use of water and energy during the manufacture of its products as well as seeking new packaging and waste reduction measures.
“We have a lot of discussions around responsible manufacturing,” explains Angela Reamer, Vice President of Manufacturing at Monin Americas. “We really work towards being as responsible and as efficient as we can with all of those resources.”
Speaking at our Data-Driven Sustainability and ESG online summit earlier this year, Reamer discussed the importance of making people the champions of your sustainability strategy and of setting the right culture to make it happen.
Here are four ways that Monin integrates sustainability into the daily work and culture of its people:
#1: Embed it into the routine:
Operations are where lofty environmental ambitions meet practical reality. Sustainability needs to be embedded into the practical, daily processes of frontline workers to help shift needle on environmental performance.
At Monin, for instance, that means discussing water usage during daily manufacturing meetings.
“Depending on how our flavors are scheduled throughout the day we can either use more or less water, so we have those discussion around how we optimize from a water usage standpoint,” Reamer explains.
#2: Make data visible:
A well-established management tenet is that ‘what gets measured, get managed.’ Sustainability is no different. Data should be easily accessible, updated regularly and shared throughout the organization. Transparent data helps to keep sustainability front of mind and identify how the company is doing against its goals.
At Monin, the company is implementing a digital platform for downtime and waste tracking. Reamer says that the platform will incorporate real time data and will help to create that visibility among frontline staff.
It’s important to “bring the data to the forefront and have it visual and get everyone involved,” she explains. “Everyone has an important role within sustainability. That goes with safety and quality as well.”
READ: How Industry 4.0 Can Help Manufacturers Reduce Carbon Emissions
#3: Encourage workers to challenge the status quo (in a positive way):
Frontline workers are closest to the operational processes and procedures that enact a company’s strategy. Just as these workers often have the best ideas on how to improve those processes for the sake of efficiency, quality, and safety, they can also have the best ideas on reducing resource and energy use.
Reamer says that Monin tries to build up a culture where workers feel safe to flag up problems and challenge the way that work gets done to find new and improved ways of doing things.
That means tracing the root cause of problems back to processes and building trust within the team so that people are comfortable sharing what can be improved.
“If something happens, it’s all about the problem solving and finding a solution together,” she explains. “We’re people, we’re going to make mistakes.”
#4: Ensure leaders walk the talk:
One of the fastest ways of undermining sustainability initiatives is to have leaders that don’t model the behaviors and mindset needed. “Do as I say and not as I do” has never been a winning formula.
Reamer says that performance evaluations are based on concrete metrics and the company’s mission and value, which include an ESG component. Leaders are evaluated based on how they exhibited those missions and values.
Interested in Learning More?
Join over 200 of your industry peers as they advance clean manufacturing and reinvigorate America's industrial sector at our upcoming Decarbonizing America's Industrial Sector summit taking place 13-15 September 2022. Find out more here.